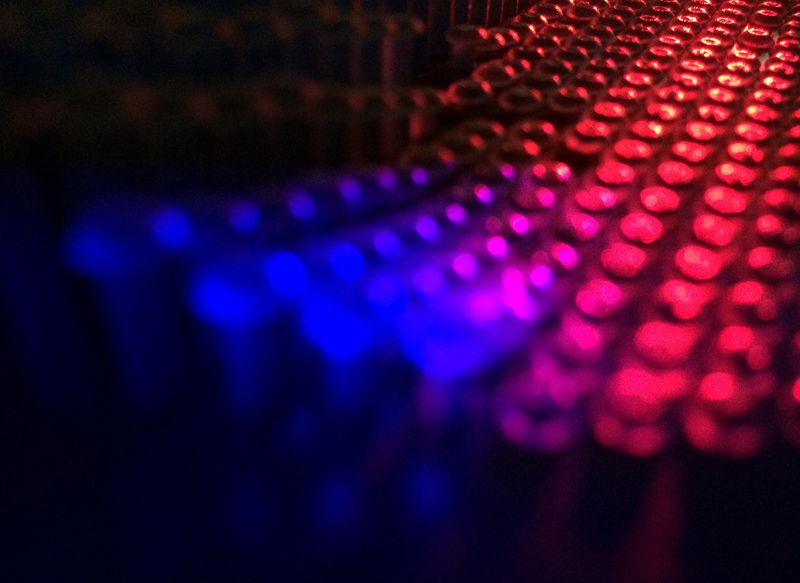
Rapid Prototyping, also referred to as additive manufacturing or 3D printing, is an advanced technique that makes it possible to produce functional parts from digital designs rapidly and affordably. Product development has been revolutionized thanks to this revolutionary process, which empowers engineers, designers and manufacturers alike to realize their ideas quickly and precisely.
Rapid Prototyping has revolutionized how mechanical engineers approach new product development. This revolutionary technique has significantly shortened design and testing cycles by providing rapid fabrication of physical models from computer-aided design (CAD) data.
Rapid prototyping techniques encompass several techniques, such as stereolithography, fused deposition modeling and selective laser sintering; each offers its own specific advantages for various industries and applications. In this article, we cover all about Rapid Prototyping, Rapid Prototyping techniques as outlined by their types.
Rapid Prototyping
What is Rapid Prototyping? Rapid Prototyping, powered by 3D computer-aided design (CAD), quickly produces physical components or assemblies using additive manufacturing - more commonly referred to as 3D printing - without incurring high manufacturing costs. Based on how closely its designed object resembles its final result, rapid prototypes may either be classified as high-fidelity or low-fidelity prototypes - the former will closely resemble their intended end product, while low-fidelity prototypes exhibit substantial deviations.
Rapid Prototyping refers to an umbrella term covering methods to fabricate scale models of physical parts or assemblies rapidly from three-dimensional CAD data, producing tangible or visual representations for use in testing, evaluation, and refinement purposes. Rapid prototyping serves an invaluable purpose of creating real visuals of design proposals as tools for testing purposes as quickly as possible.
How Rapid Prototyping Works
Rapid Prototyping (RP) encompasses various manufacturing techniques, with additive manufacturing being its cornerstone. However, rapid Prototyping also incorporates techniques like high-speed machining, casting moulding, and extruding as additional techniques. While additive manufacturing remains primary when creating prototypes, conventional processes may also be utilized; subtractive methods include milling grinding turning as well as compressive ones where semi-solid or liquid material can be moulded into its desired form before solidification such as casting compressive sintering moulding can all play their roles when creating prototypes.
Want More Information About Our Services? Talk to Our Consultants!
What Makes Rapid Prototyping Important?
Companies need to develop and introduce new products faster in today's rapidly evolving consumer market if they want to remain competitive, which makes rapid Prototyping essential. Rapid Prototyping achieves three primary goals of product development.
- Rapid Prototyping plays an essential part in speeding up product creation processes as it streamlines new product development procedures. It has proven extremely valuable when creating successful products since rapid Prototyping allows faster new product development cycles than conventional means can achieve.
- Early design/concept validation includes testing the form, fit and function of designs in early design/development stages.
- Final product validation against technical requirements and business goals
- Functional testing helps validate the objectives of concept designs and define product specifications.
- A prototype provides end users, clients and customers with a hands-on user experience. It allows for feedback gathering from participants in an end-user forum.
Techniques For Rapid Prototyping
Techniques for Rapid prototyping encompass:
- Additive Manufacturing: Additive manufacturing, commonly referred to as 3D printing, is an increasingly popular rapid prototyping technique used for rapid development. It involves building objects layer by layer using various materials - adding material only where required - making the method highly pliable and suitable for creating complex geometries. Various plastics, metals, and composite materials may be utilized through additive manufacturing for an array of applications.
- Deterring Manufacturing Costs: Subtractive manufacturing refers to the practice of subtracting material from solid blocks by milling, grinding or turning techniques in order to form desired shapes. It can be especially helpful when working with materials like metal and ceramic, producing precision components or prototypes with tight tolerances.
- Productive Manufacturing Systems: Compressive manufacturing techniques involve moulding semi-solid or liquid materials into prototypes using casting, compressive sintering and moulding processes. Such approaches are especially advantageous when working with rubber parts, ceramic components or certain plastic parts that require maintaining specific material properties or intricate shapes. For instance, rubber rings and plastic parts with exact dimensions need to be produced at certain angles and maintain specific material properties while being made smoothly without ripples and imperfections.
- High-Speed Machining: High-speed machining (HSM) is an industrial subtraction manufacturing technique using sophisticated machinery and cutting tools to rapidly shape materials at high speed, often for precision applications that involve fine details or intricate designs that cannot be machined directly by other means. HSM may be applied to both metal and plastic materials.
- Casting: Casting is the process in which liquid material, usually metal or plastic, is poured into a mould to produce prototypes for components that require high strength, intricate details or precise reproduction of shapes; casting processes are commonplace within automotive and aerospace industries.
- Moulding: Moulding techniques involve shaping semi-liquid or viscous material within a mould. This technique can create prototypes in various sizes, from intricate parts to larger structures, often found in toys and consumer goods manufacturing industries.
Read More: Rapid Prototyping Slashes Mechanical Engineering Costs - $3m+ Savings Await
Various Types Of Rapid Prototyping
Rapid Prototyping includes several types. They are:
- Stereolithography (SLA) Or VAT Photopolymerization: SLA (stereolithography) was one of the earliest commercial 3D printing techniques. This design process involves solidifying layers of photosensitive liquid using UV lighting that's controlled by a computer.
- Selective Laser Sintering (SLS): SLS printing technology can produce metal and plastic prototypes using layer-by-layer construction using laser heat to sinter powdered material, producing components layer by layer using laser heating and sintering technology. Although strength may differ slightly between SLA parts and those made using SLS technology, post-processing may often be necessary due to surface roughness issues.
- Fused Deposition Modelling (FDM) Or Material Jetting: FDM 3D printers use Fused Deposition Modeling (FDM). FDM uses thermoplastic filament that is melted and extruded layer by layer to produce 3D models according to computer instructions, typically producing limited but cost-effective results in real product development. Although early FDM results had limitations, current-generation printers offer improved outcomes, which make this technique worthwhile and cost-effective for product creation.
- Selective Laser Melting (SLM)/Powder Bed Fusion: SLM (Stereolithography Layer Manufacturing), used for high-strength and complex parts, involves melting fine metal powder layer by layer with an intense laser or electron beam, providing access to multiple materials simultaneously. SLM technology has gained wide adoption by industries including aerospace, automotive, defense and medical.
- Laminated Object Manufacturing (LOM) Or Sheet Lamination: LOM builds parts by stacking thin laser-cut laminate sheets layer by layer, which may require less advanced equipment but doesn't necessitate controlled conditions for production.
- Digital Light Processing (DLP): Similar to SLA, DLP polymerizes resins using conventional lighting sources. While faster and cost-efficient than its SLA equivalent, it requires additional support structures and post-curing steps for success.
- Continuous Liquid Interface Production (CLIP): CLIP continually pulls parts from a vat and modifies their configuration using an optical light barrier in order to form cross-sectional patterns on plastic sheets.
- Binder Jetting: Binder Jetting is another method used for printing multiple parts quickly at once; however, they may not be as robust. Binder Jetting uses a powder bed onto which liquid droplets bond particles together into layers for this method of production.
Rapid Prototyping's Advantages In Mechanical Engineering
- Reduced Time to Market: Engineers can iterate and refine designs in a fraction of the time typically needed by using rapid prototyping techniques.
- Cost Savings: By removing the need for pricey moulds and tooling, rapid prototyping results in significant cost savings.
- Increased Design Flexibility: Engineers are able to quickly and easily create new functional prototypes and make changes to existing designs.
- Better Communication: Engineers, stakeholders, and end users can better visualize and comprehend the product with physical models, which facilitates more productive feedback and teamwork.
- Risk Reduction: Potential problems can be found and fixed early in the rapid prototyping process, which lowers the chance of expensive design errors.
The Disadvantages Of Rapid Prototyping
- Lack of accuracy: Rapid prototype parts and assembly may not be able to achieve the same accuracy if the product's functionality significantly depends on the accuracy of the details.
- Additional upfront expenses: Because of the technologies involved and the need for a quicker turnaround, rapid Prototyping is expensive.
- Certain rapid prototyping techniques remain costly and inefficient.
- diminished strength and surface finish of the material
- Skilled labor was needed for rapid Prototyping and limited material selection.
- Prototype testing is impacted when important features are disregarded because they cannot be prototyped.
- End-user bewilderment, clients believing it to be the completed project, or developers misinterpreting user goals
Want More Information About Our Services? Talk to Our Consultants!
Conclusion
Rapid Prototyping has revolutionized mechanical engineering. Better finished products, lower costs and quicker time-to-market are the hallmarks of success thanks to this technique that enables engineers to turn ideas quickly and cost-effectively into tangible models. Rapid Prototyping services have quickly become an indispensable asset within mechanical engineering practice as technology evolves further - its capabilities are only set to increase over time as more engineering tools emerge and adaptable hardware solutions become available.