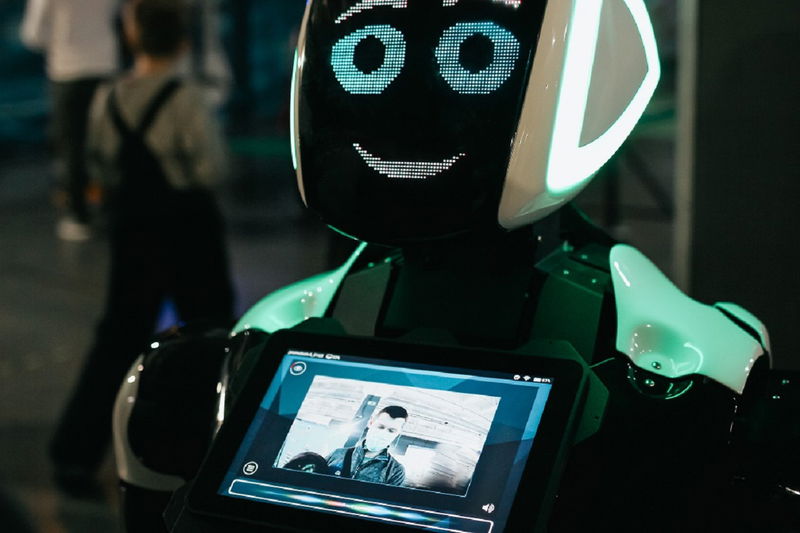
Rapid prototyping refers to the practice of rapidly creating physical components from three-dimensional designs in an economical and timely fashion.
Designers and engineers can benefit from rapid prototyping by rapidly iterating between digital designs and physical prototypes numerous times to produce more end products through rapid prototyping.
Everybody can now easily transform ideas into realistic proofs of concept that closely resemble finished goods thanks to rapid prototyping tools, before developing prototypes with high fidelity that truly reflect finished goods with 3D printed prototypes at affordable costs allowing teams to rapidly produce multiple usable prototypes at once.
This article will introduce the benefits and principles of rapid prototyping as well as 3D printing to help create prototypes faster and more affordably, along with real world examples from top businesses.
What Is Rapid Prototyping?
People should recognize they're not communicating via an end product to collect honest testing criticism, rather they need to understand they are communicating via prototype. Once people realize it's just a prototype they tend to give proactive suggestion responses rather than genuine reactions which is the true litmus test for the viability of a prototype. A clickable prototype with real data such as photographs will do nicely here
Certain events must take place for high-fidelity prototypes to become feasible; otherwise they resemble what's inside more closely than anything else could. Product teams must first consider all scenarios customers could take when engaging with the prototype; next step: drawing from real technical and UX skills while brainstorming ideas into reality in just an afternoon.
Wireframing provides an interim solution when building out an entirely realized prototype is too early or costly, providing product executives with an option for quickly producing sketches that capture workflow ideas and fundamental user interface concepts.
Wireframe-based tests can assist manufacturers in understanding what components must be in place in order to create an "effective enough" working model, and are ideal for real customer testing. It ensures all variables that matter for testing purposes, shortening procedure times; although often product teams must leave implementation details to development or UX teams.
Accessible websites - also referred to as exterior prototyping - can be rapidly created using various design and user experience tools by team members who are willing to settle for prototypes that fall somewhere between wireframes and fully functioning designs. Although such prototypes won't contain as much real data as fully functioning designs would, they provide invaluable user input on various solution components. Fast testing methods include creating multiple prototypes for simultaneous user testing - this enables teams to definitively determine whether Option A truly surpasses Option B.
Rapid Prototyping Vs Prototyping
Designing prototypes is an integral component of creating effective projects; yet for some it was an impediment to success. Product designers and engineers would use simple tools to improvised assemble proof-of-concept models; but similar procedures were often necessary to produce working prototypes and parts suitable for manufacturing. Low volume, specific models can often prove prohibitively expensive due to costly tooling setup and setup for conventional production methods like plastic injection molding.
Rapid prototyping offers businesses the means of quickly turning ideas into workable proofs of concept, creating high-fidelity models which closely resemble finished goods in appearance and functionality, then going through various validation phases before mass-producing the model. Rapid prototyping gives designers and architects more quickly produce prototypes from renderings created with CAD software than ever before, as well as quickly make any necessary modifications based on opinions or examination in the real world.
Rapid Prototyping Tools And Methods
3D printing and additive design have become synonymous with rapid prototyping. There are various 3D printing techniques for rapid prototyping; FDM (fused deposition modeling), stereolithography (SLA), and selective laser sintering (SLS) are among the more frequently employed ones for rapid prototyping purposes.
Fused Deposition Modeling (FDM)
Fused Filament Fabrication (FFF), commonly referred to as fused Deposition Modeling (FDM), is a 3D printing method which produces parts through melting and extrusion of thermoplastic filament that is then slowly laid down layer by layer in a build area using a printer nozzle. FDM 3D printing has quickly become the go-to type among consumers due to the rise of hobbyist 3D printers, yet engineers and designers also enjoy using FDM printers with expert skills.
FDM 3D printing offers lower recovery and reliability compared to other plastic 3D printing techniques, making it unsuited for producing delicate components or intricate designs that need high levels of detail. Mechanical polishing techniques may produce higher-caliber finishes. Some experienced FDM printers utilize soluble supports as a solution.
FDM printers can work with more advanced engineering thermoplastic materials and composites as well as standard thermoplastics such as ABS, PLA and their respective blends, but are especially advantageous when producing quick prototypes of simple parts, which would typically require machining.
Stereolithography (SLA)
With photo SLA 3D printers can use laser technology to turn liquid resin into hardened plastic material for curing. SLA is considered an industry standard due to its superior image quality, accuracy and material versatility - something experts often appreciate about SLA. SLA 3D printing makes available an extensive variety of compounds with optical, mechanical and thermal properties for rapid prototyping purposes.
SLA parts stand out among plastic three-dimensional printing methods as having the highest resolution and accuracy, most defined details, and smoothest surface finish compared to its competitors. SLA makes for ideal prototypes requiring tight tolerances that showcase these characteristics - this makes SLA an excellent way to produce high fidelity look-a-likes or functional works-likes prototypes with impressive detail.
SLA stands out due to the versatility of its resin library. Goods suppliers have developed SLA photopolymer resin formulations featuring wide-ranging chemical, physical and thermal characteristics reminiscent of norm and technology thermoplastic materials for production thermoplastic applications. SLA 3D printing with Draft Resin can be one of the fastest prototyping methods; its speed often outpaces FDM three dimensional printing by up to 10 times.
Selective Laser Sintering (SLS)
Laser melting additive manufacturing technology has long been considered one of the premier industrial practices, beloved by designers and makers across multiple sectors due to its proven track record in producing strong yet functional components.
SLS 3D printers use lasers to fuse tiny powdered polymer particles together into solid objects. While printing, your part is supported by unfused powder which doesn't need additional support structures - making SLS ideal for intricate shapes like cuttings, thin walls, interior features or negative features that need minimal support structures for support during printing. SLS printed parts also boast superior mechanical properties and strength comparable to injection-molded components. Strong works-like prototypes and engineering prototypes that undergo thorough functional examination for goods can be created through SLS 3D printing.
SLS 3D printing is often utilized in rapid prototyping applications for works-like prototypes and engineering prototypes designed for rigorous functional testing of products (like air ducts ) as well as expanding customer input.
Read More: Revolutionizing Mechanical Engineering: The Impact of Automated Systems and Robots
Benefits Of Rapid Prototyping In Mechanical Engineering
Rapid prototyping has completely revolutionized how mechanical engineers approach designing newer products. This technique has significantly reduced time and expense related to engineering by providing rapid fabrication of physical models from computer-aided design (CAD) data. Below are some benefits of rapid prototyping in mechanical engineering:
Realize And Explore Concepts Easily
Rapid prototyping allows designers to transform original concepts quickly into low-risk concept explorations with the appearance of finished goods, without going beyond virtual visualization and making virtual models available to compare side by side concept comparison and understand its overall feel and appearance.
Communicate Ideas Effectively
By conveying their ideas through physical objects, creators are better able to convey concepts to collaborators, clients and peers than with mere screen visuals alone. Quick prototyping makes it simpler for designers to collect the precise and useful user feedback required to comprehend user needs and enhance or modify designs accordingly. Test of an accessory designed with Form 3 SLA 3D printer after it has finished production.
Save Cost And Time
3D printing eliminates the need for expensive tooling as different shapes can be produced using identical equipment. Local prototyping reduces both lead times and expenses associated with outsourcing services.
Design Iteratively And Instantly Incorporate Changes
Final products are always the result of multiple rounds of testing, assessment, and refinement in the design process. Utilizing 3D printing as rapid prototyping enables designers to produce more realistic designs instantly while taking full advantage of learning by doing.
An effective design model involves an intensive 24-hour phase: from planning the layout while on the job to using 3D printing to producing prototype parts overnight, cleaning and testing them the following day before making adjustments for layout adjustments, adjustments made on day 3, then finally recantation of design plans and finally recitation.
Test Thoroughly And Minimize Design Flaws
Recognizing and rectifying design flaws early can save companies significant costs associated with future tool modifications or costly revisions in product manufacturing or design. Engineers can reduce risk associated with usability and manufacturability issues before producing items through rapid prototyping by conducting thorough evaluation of designs that resemble finished goods.
Conclusion
Rapid prototyping in mechanical engineering has revolutionized productivity and creativity. Thanks to rapid prototyping's speedy yet cost-cutting processes, products with increased functionality, lower expenses and quicker time-to-market have emerged thanks to this technique, simplifying product creation process by enabling engineers to transform ideas quickly into tangible prototypes affordably and quickly. Rapid prototyping tool in mechanical engineering today and its capabilities and uses continue to expand as technology develops further.