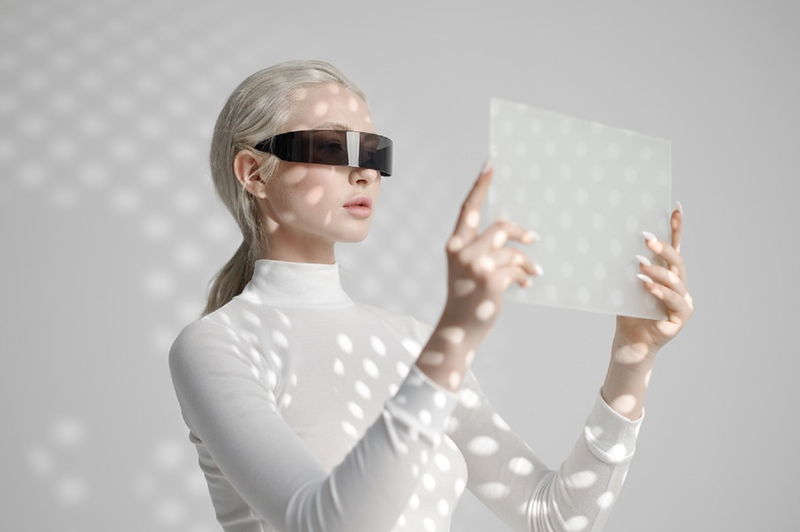
If you work with CNC equipment, you are probably involved with CAD/CAM systems or CNC programming. The most crucial development in the CAD/CAM business recently has been integration. The integration will be crucial to the development of CAD/CAM products. Large integrated CAD/CAM systems that may be operated on numerous workstations have been available for a long time. These systems combine CAD and CAM by sourcing all components from a single supplier.
A new product line is now available highlighting integration as a crucial problem. Different from merely single-brand products, they search for integration in other ways. CAD/CAM Integration: What is it? Good or bad, is it? Is it required? Everything depends on the kind of integration you require. It is important to understand the steps involved in CAD/CAM integration.
Any software that defines a mechanical component using geometry, surfaces, or solid models is called CAD. NC programs are produced by CAM software. Even though there are other CAD or CAM kinds, this essay will exclusively cover mechanical CAD/CAM.
Engineering design and production employ CAD/CAM software for three different objectives.
Design Modeling: A mechanical engineer uses CAD software to create a part. The model of this part can be derived from its definition. This model is available as a CAD data file or as a sketch.
Modeling for Manufacturing: CAD software is used by a manufacturing engineer or NC programmer for:
Create a computer model of the part you have drawn.
-
Assess and correct the design CAD data to meet manufacturing tolerances. This is a common task.
-
To allow for manufacturing, create new part models using the original design. This could include creating models or adding draft angles to the part to allow for multi-process manufacturing.
NC Programming: A manufacturing programmer or engineer employs CAM software when selecting the tools, techniques, and procedures to machine the models detailed in the manufacturing modeling section.
In a perfect world, you could select up to three items that excel at each of these tasks, and they would all work together seamlessly. This world is not ideal. High levels of integration are required for these goods to function together. The interaction between several software features is known as integration. There are three different integration types to take into account:
Data Integration: Data is the capacity to share models and pieces (common files or a shared database). For CAD/CAM, this integration is crucial. An IGES surface file is a bad illustration of data integration because it takes a lot of manual labor to be successful. As they convey data smoothly, Parasolid files sent from one Parasolid-based software program to another are excellent instances of data integration. Software applications built with Parasolid can share a single Parasolid file. This is possible because associativity and model history can both still be preserved.
Application Integration: For a single user, app integration enables various modules to function together. This can be accomplished by including various functions in the same program (or "inside" integration). This effect (CAM "beside"") can be achieved by smoothly combining two programs thanks to technology like OLE.
How Integration Began
At first, there were no CAD systems. Engineers used CAD technologies to draw parts. An NC programmer, machinist, or manufacturing engineer could program from these designs thanks to the first CAM systems. It took time and was prone to human mistakes to create drawings and program sections from them. A novel concept was developed to do away with the back-and-forth drawing process. The birth of integrated CAD/CAM.
The same brand of CAD and CAM products could be purchased through integrated CAD/CAM. Today, a lot of businesses provide these things. These products are provided by companies like Parametric Technologies (Pro/E, Pro/Manufacturing), Unigraphics (Catia), SDRC (IDEAS), Computervision, and numerous more. They all offer high-end, high-power, and expensive solutions. These products often provide data, interface, or application integration. These products are not ideal for all users due to their complexity and cost. Additionally, once a customer has chosen the CAD product that he likes, they are stuck with the product. It is not allowed to mix and match products.
Best-Of-Class Solutions
The shortcomings of conventional integrated workstation CAD/CAM systems have aided in developing the standalone CAM markets that we are familiar with today. These CAM products have a strong emphasis on either NC programming or manufacturing modeling. They are typically less expensive, quicker, and more effective than their integrated workstation-based cousins. These solutions still have an advantage in simplicity, efficiency, and cost. Still, they have advanced in sophistication to match the capabilities of conventional integrated CAD/CAM tools. They have had to contend with issues like poor interface with the CAD system and original design modeling and restricted access to the CAD market. This has started to alter.
The New CAD Market
CAD software has been stored on the PC for many years. The main applications of this CAD program were wireframe CAD and 2D drafting. A surface modeling program is Autocad. Despite the success of Autocad and related solutions, they have not been able to compete in the market for workstation CAD. There have been several changes in recent years.
The new PCs were a popular option for workstation CAD users since they were reasonably priced, simple to use, economical, reliable, and quick. Despite not being as quick as a workstation, PCs still provide outstanding value for the money compared to their performance. These PCs could run the same solid modeling technology as the major workstation CAD programs. It wasn't long before people realized this.
Another crucial development in the CAD/CAM business is the appearance of independent solid modelers. Solid modeler kernel firms Ricoh (Design base), EDS (Parasolid), and Spatial Technologies (ACIS) started selling to mid-range CAD solution providers. In 1995, SolidWorks and Intergraph SolidEdge were both released. This signaled the start of a new era for CAD solid modeling. Not everyone had success, even them. Most of the main CAD firms have announced new products to enter this industry. To be more easily recognized as a mid-range CAD player, Parametric Technology renamed the Pro/E Jr. as PT Modeler. DesignWave was introduced by Computer Vision and acquired by PTC. To provide CAM technology, SDRC established its Artisan series and purchased Carmax. Catia recently acquired SolidWorks and Dassault (Catia), which announced that they would launch a Windows NT product. Solid modeling technology fuels the rapid growth of new products. It serves as a backbone for seamless data transfer between compatible products.
Want More Information About Our Services? Talk to Our Consultants!
CAM in CAD Market
The market for CAD solid modeling products is expanding. Some CAM goods have taken the quickest route to a marketing promise supported by fact. This resulted in an "internal" version of the product's CAD program. The CAD software contains the CAM capabilities of the product. However, this might lead to a constrained set of CAM capabilities and a feature set that is less extensive than the standalone versions.
Another Windows technology that is gaining popularity is OLE (or OLE for D & M). This enables CAM products to "ask" CAD programs directly for model data without the need to save, open, or deal with translations of files. This is yet another effective instrument for data delivery and integration.
In the past, all CAD/CAM solutions that provided high levels of integration did so by integrating every function into a single program. Some individuals think that CAD/CAM software can be incorporated similarly. The conventional same-app strategy can be replaced with flexible solutions based on modern technologies. The smooth integration of many programs is made possible by solid models and OLE. Interface interaction is strong with Windows NT/95.
Who Needs Integration?
Everybody. Three types of users are Available to Illustrate the Diversity of Needs:
Job shops: A job shop fabricates designs made by others using CAD technology made by others. Job shops are not required to use CAD or primary design models. As a result, they don't benefit much from application integration or connections with other CAD systems. Data integration between CAD systems is both a useful feature and a significant issue. Job shops have to deal with a wide variety of data sources and data kinds. The ability to import and correct data from various sources is crucial. For a workshop, CAM and manufacturing modeling capabilities are crucial.
Small Integrated Manufacturing Sites: One person handling all of the product design modelings, manufacturing modeling, and NC programming on a single computer is a tiny integrated manufacturing firm. Like the job shop, data integration between goods is a major problem. Integration of the interface and application with the user's CAD product has additional advantages for the user.
General Manufacturing Sites: Individuals with specific expertise in design modeling, manufacturing modeling, and CAM work at these manufacturing sites. They typically have entirely different departments. These businesses may have job shop-like sections that support a range of internal CAD formats. For optimum integration, they can also have departments that utilize the same CAD as their design department. Data integration is a frequent issue.
Read More: The profit of CAD/CAM Software for Woodworking at Home
How to Decide What's Best For You
The first step in choosing which storage system is best for you is realizing that you have options. There are numerous solutions if you decide the system is not ideal. Using independent products doesn't mean you have to accept subpar data translations. Look at what you need. Do you primarily obtain your CAD files from a single or several sources? Do you mostly obtain CAD files from one source? Next, find CAD and/or CAM products that best meet the requirements of your shop. This should involve emphasizing usability and suitability for the task you conduct. You now have all the knowledge and cutting-edge tools necessary to make an educated decision.
Let's Take a Look at Five Benefits that Integrated CAD/CAM Systems Offer:
Remove CAD and Data Translation Mistakes
Integrated CAD/CAM Systems eliminate costly extra data translations between CAD applications and CAM programs that work on the same 3D model. Data translation can be a problem with standalone systems. Version issues and version lags are also possible. Sometimes, the CAD file version is different from what the CAM system expects to see. This can lead to errors.
Integrated CAD/CAM allows for true associative machine or model association. This allows for design modifications to be automatically updated in the CAM data. This eliminates the need to rework the CAM system due to time-consuming design changes. Data translation errors avoid multiple disconnected files to maintain
Keep your Files Organized
Both CAM and CAD are distinct files that must be maintained. However, it is difficult to keep two programs' files up-to-date. The CAM file should be updated when design changes are made. If necessary, the CAM portion must also be reprogrammed.
Integrated CAD/CAM systems organize your data so that you can work in teams and work in parallel. You can also react more quickly to design changes. These systems include file management and repositories that allow everyone to work on the most recent design iteration. A master model with associativity makes it possible to analyze, simulate, and update cutter paths faster without worrying about version conflicts.
Simple Workflow
Standalone CAM systems tend to be process-based rather than feature-based programming. Selecting the right tool is the first step.
You can create operations such as rough milling a pocket. Once the parameters for speed, feed, and any other cutting parameters, including depth, are entered into the system, the process is created. The system then selects another tool, such as a pocket finishing tool. All previous steps are then repeated to create another process. After completing the process, you can simulate the program and post-process it to create the G code needed for the manufacturing operation.
Programmers are accustomed to treating each part of a standalone CAM program as unique, even if it shares features with other parts that have been programmed and machined. Every programmer might have a different way of programming this part. Standalone CAM systems encourage this approach. The result is five different programmers with five inconsistent programs.
An integrated CAD/CAM software eliminates data translation. The same interface for design and manufacturing allows for a simpler design-to-manufacturing workflow. This allows for a shorter training time and fewer IT resources to maintain multiple CAD/CAM software packages. It also makes the process more robust.
Simplified workflow for reduced training time, fewer IT resources, and a stress-free work environment
Automate Manufacturing Processes
Standalone CAM systems can be disconnected from industry-leading solutions such as SOLIDWORKS. Therefore, integrated CAD/CAM automation cannot be provided. You can take advantage of automation by using the integrated CAD/CAM feature in HCL CAMWorks. To create the most efficient tool paths, you can use tolerances, product manufacturing information (PMI), and surface finish information (PMI) to automatically create CNC programs.
Integrated Validation Tools
Modules for validating designs are often included in integrated CAD/CAM systems before beginning machining operations. Few integrated CAM systems can perform G-code machine simulation directly within the CNC programming environment. This eliminates the need for dry runs to validate programs and reduces setup time. After the program is simulated from the Gcode, it can be run on the machine. These validations or simulations can help avoid costly machine collisions and programming errors, reduce scrap, and improve overall quality.
In addition to the five main benefits, integrated CAD/CAM allows for better collaboration between manufacturing and design departments. This knowledge can ensure that designs are done correctly the first time. It is crucial to address designs for manufacturability requirements to meet program schedules, improve quality, reduce errors, and rework, and control manufacturing costs. It's easier for programmers and designers to work together using the same system.
CAMWorks was the first CAM system to be fully integrated into SOLIDWORKS. CAMWorks is a leader in Automatic Feature Recognition and Interactive Feature Recognition (IFR). CAMWorks allows for true associative machining - automatically adapting to changes to the part model.
CAMWorks is seamlessly integrated with SOLIDWORKS and allows you to:
-
You can use and manage one file for both the CAD and CAM systems.
-
You can use the CAMWorks machining tree, commands, and tools at the click of a button, along with SOLIDWORKS, to generate tool paths.
-
To ensure that the part you machine is identical to the one you model, use the same SOLIDWORKS geometry for creating toolpaths
-
Reduce the time and effort required to transfer files using standard file formats like IGES or STP
Want More Information About Our Services? Talk to Our Consultants!
Conclusion
A fully integrated CAD/CAM solution such as CAMWorks creates a bridge between design and manufacturing teams. This allows the user to have complete control over both the design and manufacturing process. The integrated CAD/CAM environment allows users to benefit from solids-based and fully associative CNC machine machining.