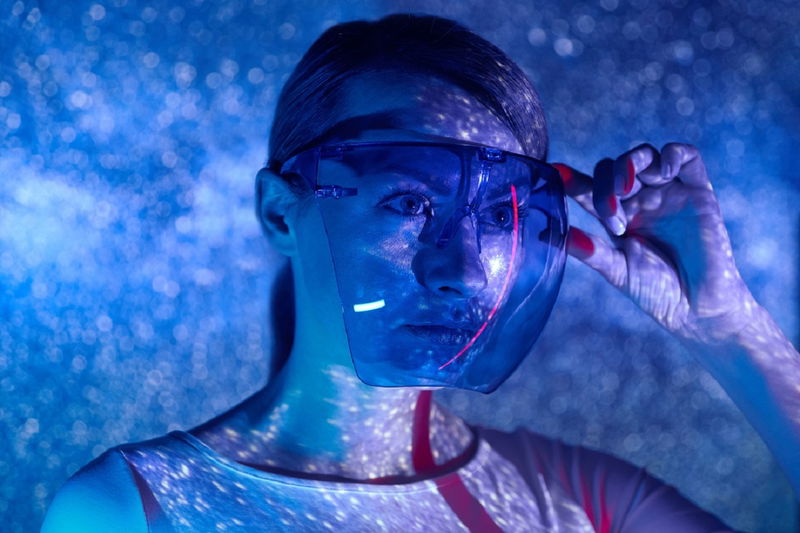
Software tools have become essential in mechanical engineering for designing, analyzing, simulating, and optimizing many elements of mechanical systems. In addition to increasing productivity, these tools allow engineers to tackle complex problems accurately and creatively, something seasoned and novice engineers can benefit from. This blog post presents the top mechanical engineering software tools experienced and budding talented engineers should use.
Computer technology has proven essential in creating mechanical goods with superior performance levels through supporting design procedures and performing system analysis in mechanical design. Below is a list of 8 popular mechanical engineering design software programmes used worldwide. Do you use any of them as mechanical engineering specialists?
What Exactly Is Mechanical Design Software?
Engineers and designers can produce intricate technical drawings using mechanical design automation software (MDA). These diagrams include all engineering specifications related to an item of machinery, product, component or part, including tolerances, materials used, measurement procedures that might need to take place, and more. Mechanical engineers rely on technical drawings to communicate with production workers when planning machinery manufacturing or production operations.
Engineers and designers using mechanical design software can now create highly accurate mechanical drawings in two dimensions, such as "pen and ink" sketches or three-dimensional, lifelike models, using 3D CAD modeling software, eliminating manual drawing as part of their daily workloads. Mechanical design software makes manual drawing obsolete!
Engineers and designers can utilize technology to quickly test and develop new concepts without wasting their time or resources. Skilled mechanical engineers and machine designers around the globe rely on Dassault Systemes' innovative drafting and design solutions for precision mechanical engineering firms work as industry leaders for over four decades!
8 Software Tools That Every Mechanical Engineer Needs
These are the top eight software tools for mechanical engineering:
AutoCAD
Autodesk introduced computer-aided design (CAD) technology through AutoCAD in 1982, dramatically changing computer-aided engineering projects practice and impacting design projects across many sectors. Since then, this CAD platform has proven vital in designing projects across numerous industries and disciplines.
CAD software solutions, which provide development software for parametric modeling, simulation analysis, and product documentation, are the industry standard in product design. Before products are built on Earth, they must be drawn or modeled on paper using this type of CAD software, so we know precisely how we intend to make them in the 3D form in the 2D or 3D form before their construction can commence.
Applications And Features Of AutoCAD
AutoCAD offers engineers an ideal platform for producing accurate 2D and 3D models of mechanical parts, assemblies, and structures and more easily visualizing, analyzing, and communicating their ideas through precise designs. Thanks to its powerful drafting and modeling tools, engineers can more efficiently visualize, analyze, and communicate ideas through precise designs than before. Manufacturing facilities use this versatile program alongside buildings as it adheres to industry standards while streamlining design with its extensive library of symbols and block templates.
Characteristics And Effects
AutoCAD features an intuitive user experience and supports third-party plugins for parametric design, making this a valuable engineering resource for engineers of all disciplines. Engineers may create realistic 3D models of complex mechanical systems using their 3D modeling tools while their parametric restrictions facilitate effortless changes and adaptation, thus guaranteeing efficient design iterations. Furthermore, cloud collaboration, smartphone access and improved rendering have increased its utility over time, making AutoCAD even more valuable in today's engineering operations.
SolidWorks
SolidWorks, first released by Dassault Systemes in 1995 and rapidly adopted for mechanical engineering design purposes, has quickly become one of the premier 3D CAD platforms available today.
Applications And Features Of SolidWorks
SolidWorks engineers can quickly create accurate 3D models of mechanical assemblies and components for simulation and visualization purposes, aiding simulation and visualization processes. With integrated simulation and analysis tools that allow engineers to forecast performance forecasting, quick design updates/modification capabilities, and parametric modeling features that enable quick design updates/modification, SolidWorks makes its mark across industries, including consumer goods, automotive, aerospace, etc., while encouraging creativity and effective product creation processes.
Characteristics And Effects
SolidWorks software's sophisticated surface, sheet metal design and rendering toolset enhance designs with greater detail. Engineers can verify structural integrity by performing stress, temperature, and fluid flow assessments with its simulation features; engineers can also ensure their designs have reliable structural integrity through stress temperature flow assessments using SolidWorks simulation capabilities to evaluate stress temperatures or fluid flows within designs. SolidWorks facilitates interdepartmental collaborations while speeding the design-to-manufacturing process by connecting to other PLM (Product Lifecycle Management) technologies, simplifying collaboration efforts between designers
ANSYS
Ansys revolutionized mechanical engineering projects analysis and testing via virtual testing software.
Applications And Features Of ANSYS
ANSYS provides talented engineers with a full suite of simulation features, including finite element analysis (FEA), computational fluid dynamics (CFD), electromagnetic simulations, and virtual testing and optimization services, which comprise its comprehensive simulation platform. Engineers use it to assess how mechanical designs perform under various conditions such as fluid flow, thermal impacts and stress forecasting variables like fluid volume. Virtual testing and optimization allow virtual prototype development without incurring actual prototype costs or delays. In contrast, virtual prototyping allows virtual testing at reduced development expenses and time commitments.
Characteristics And Effects
ANSYS provides sophisticated modeling and meshing tools for complex geometries. At the same time, its solver capabilities offer realistic simulations of real-life situations. Engineers can investigate relationships among many physical events thanks to its multiphysics features, which provide detailed design insights that impact sectors, including electronics, automotive, energy, and aerospace industries.
Also Read: Revolutionizing Mechanical Engineering: The Impact of Automated Systems and Robots
MATLAB
MathWorks' MATLAB made waves in the late 20th century when it emerged as a computing powerhouse capable of revolutionizing numerical analysis and algorithm development.
Applications And Features Of MATLAB
Mechanical engineering relies heavily on MATLAB, an environment for high-level programming that helps engineers simulate dynamic systems, create control systems, process signals, and analyze data quickly and effectively. Engineers utilize its significant functions and toolbox library to tackle problems rapidly across a wide range of engineering fields. Furthermore, its flexible platform facilitates research, design, prototyping, and analysis by quickly simulating mechanical systems and enabling rapid prototyping.
Characteristics And Effects
Engineers rely heavily on MATLAB as it offers an interactive and user-friendly environment for quick method development and testing, data visualization and interpretation, seamless experimental settings integration thanks to compatibility with external hardware/applications, and finding applications in automotive, aerospace and robotic industries beyond academia. MATLAB's impact can also be felt beyond academia with applications found across numerous other sectors, including automotive, aerospace and robotics industries.
Pro-Engineer (Now Creo)
PTC pioneered parametric 3D modeling when Pro-Engineer, later known as Creo, first emerged in 1987. When introduced, Creo revolutionized parametric modeling.
Applications And Features Of Creo
Creo is an invaluable product design, analysis and simulation solution that offers engineers access to various tools. Associative models with parametric modeling allow engineers to produce associative designs that automatically update when modifications occur quickly. From consumer goods to industrial equipment, Creo has proven its worth across industries with complex designs where efficient teamwork is crucial.
Characteristics And Effects
Creo features direct modeling, sheet metal 3D design and advanced surfacing as tools within its feature-rich toolbox. Mechanical, electrical engineers and software specialists alike may work more effectively thanks to Creo's multidisciplinary collaboration capabilities; product lifecycle management (PLM) and design automation processes are made more efficient through integration between Creo and PLM or PDM systems, providing efficient data management processes.
Unigraphics (Now Siemens NX)
Unigraphics (now Siemens NX), developed by Siemens PLM Software and released for public use during the 1980s as a comprehensive product design and engineering solution, saw immense popularity as part of an integrated solution set for product engineering projects.
Applications And Features Of Siemens NX
Siemens NX offers engineers engineering team analysis, manufacturing, and product design tools. Engineers can use its extensive simulation features, surface modeling capabilities and parametric modeling tools to design intricate mechanical systems using its parametric modeler and parametric simulation features. Engineers may utilize Siemens NX in sectors where precision and creativity are vital, such as consumer products and automotive or aerospace production environments.
Characteristics And Effects
Siemens NX offers capabilities that span every stage of product lifecycle management from conception to production, from analysis and optimization through simulation tools to improved performance of their product. Engineers may use the digital twin technology of Siemens NX for real-time maintenance and monitoring purposes, allowing engineers to model physical objects virtually while realizing real-time maintenance requirements and monitoring.
CATIA
Winning CATIA stands for Computer-Aided Three-Dimensional Interactive Application from Dassault Systemes, an innovative software suite first released for use during mechanical system design during the 1980s.
Applications And Features Of CATIA
CATIA provides an expansive toolkit for 3D modeling, surface design, simulation, and cross-disciplinary collaboration in many industries, including industrial design, automotive, and aerospace, where complex ideas require creative approaches and solutions.
Characteristics And Effects
Engineers can produce intricate designs using CATIA's parametric and feature-based modeling capabilities. At the same time, its integrated simulation tools help them examine and improve mechanical systems for dependability and performance. Furthermore, its collaborative features encourage effective product development by promoting collaboration across various disciplines.
LabVIEW
Laboratory Virtual Instrument Engineering Workbench, created by National Instruments, is an effective software platform for testing, measuring and controlling systems.
Applications And Features Of LabVIEW
Mechanical engineers can leverage LabVIEW for real-time data collection, analysis, and control applications in many fields, including automation, research, and experimental setups.
Characteristics And Effects
Engineers can quickly automate complex measuring systems and design user interfaces without traditional coding through LabVIEW's graphical programming method, making their work more uncomplicated than ever before. Thanks to its broad range of hardware compatibility, skilled engineers may integrate it easily into experimental setups while performing real-time data analysis, control, and monitoring in real-time. LabVIEW's vast reach extends from academic institutions and research centers to businesses that depend on accurate measurements for accurate control.
These software programs offer specific functions and uses and have become essential parts of mechanical engineering practice. Engineers who utilize them can now push innovation further while developing cutting-edge mechanical systems that shape our environments-from design through thermal analysis, simulation, and manufacturing.
Conclusion
Modern mechanical engineers rely on software tools such as those provided by mechanical software tools for numerous advantages, including better design quality, lower costs, quicker development cycles and increased teamwork. With industrial demands, new trends, and technological breakthroughs driving development forward rapidly in this mechanical engineering software development sector, its use will only become ever more essential as time progresses.
Outsource mechanical engineering services for your company at LHI. As industries and technology advance, mechanical engineering software should continue adapting to trends that enable engineers to design processes more efficiently and create with greater precision than ever. Finding a software option best tailored for you can tremendously impact productivity, efficiency, and job quality; with many available to you, all variables must be carefully considered before selecting one over another.